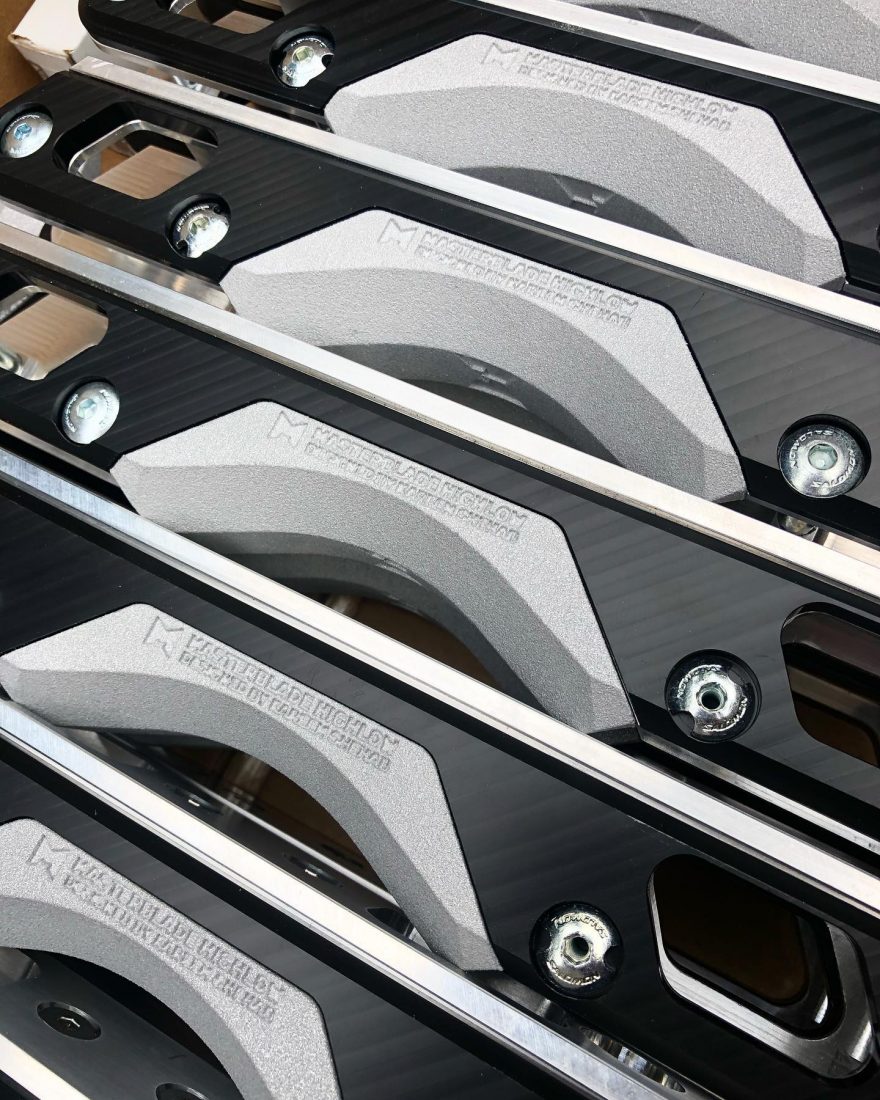
INTRODUCTION & INTERVIEW BY EDITOR-IN-CHIEF: KEVIN LITTLE @KEVINMLITTLE
With the blading resurgence in full swing, the aggressive blading market has never had so many options for potential customers as we do currently. From flat rocker, anti-rocker, freestyle and powerblading frames, there are numerous options available for skaters depending upon their skating style and personal preferences. And now, another frame company enters the fray by the name of Masterblade, which is spear-headed by long-time blader and engineering wizard, Kareem Shehab.
We had the opportunity to speak with Kareem about the research and development process behind the Masterblade frame and what steps led to him creating one of the most unique blading frames on the market today.
Kevin Little | Thank you for taking the time to speak with us today, Kareem. You have quite an extensive history within the skating world but for those that may not know you, can you give us a quick rundown of your skating roots and background?
Kareem Shehab | Thanks for the opportunity to talk about my new skate project! I’ve been aggressive skating for close to 25 years now and started when I lived in the middle east as a kid. My family moved to the US in 2000 and since then I’ve been part of the New Orleans, San Diego, Atlanta and now Seattle skate scenes. I have a bachelors degree from UC San Diego and a masters degree from Georgia Tech, both in mechanical engineering with a focus in design and manufacturing. Professionally, I started my journey as a design engineer in the cycling industry and have been working in the aerospace industry for almost 10 years now.
KL | Can you give me a little insight into what prompted you to pursue a mechanical engineering degree and how it led your current position at the aerospace company that you are working with?
KS | I had always enjoyed math and science (especially physics) courses when I was in school and I always liked building things so pursuing a mechanical engineering degree seemed like a logical choice when going to college. I became a sponsored cyclist in my early 20’s and the company I rode for allowed me to design my own pro model bike as well as help with other bike and component designs. Also around this time, I was in graduate school pursuing my masters degree and was mentoring under Mark McJunkin, who was a professor at my university and also a design engineer at L.H. Thomson, a leader in US made bicycle components manufacturing. Learning from Mark really solidified my desire to be a design engineer. Between this experience and my degrees in mechanical engineering I was able to land a job at my current company as a design engineer in research and development.
KAREEM SHEHAB PROFILE INTRODUCING THE NEW MASTERBLADE HIGH LOW FRAME
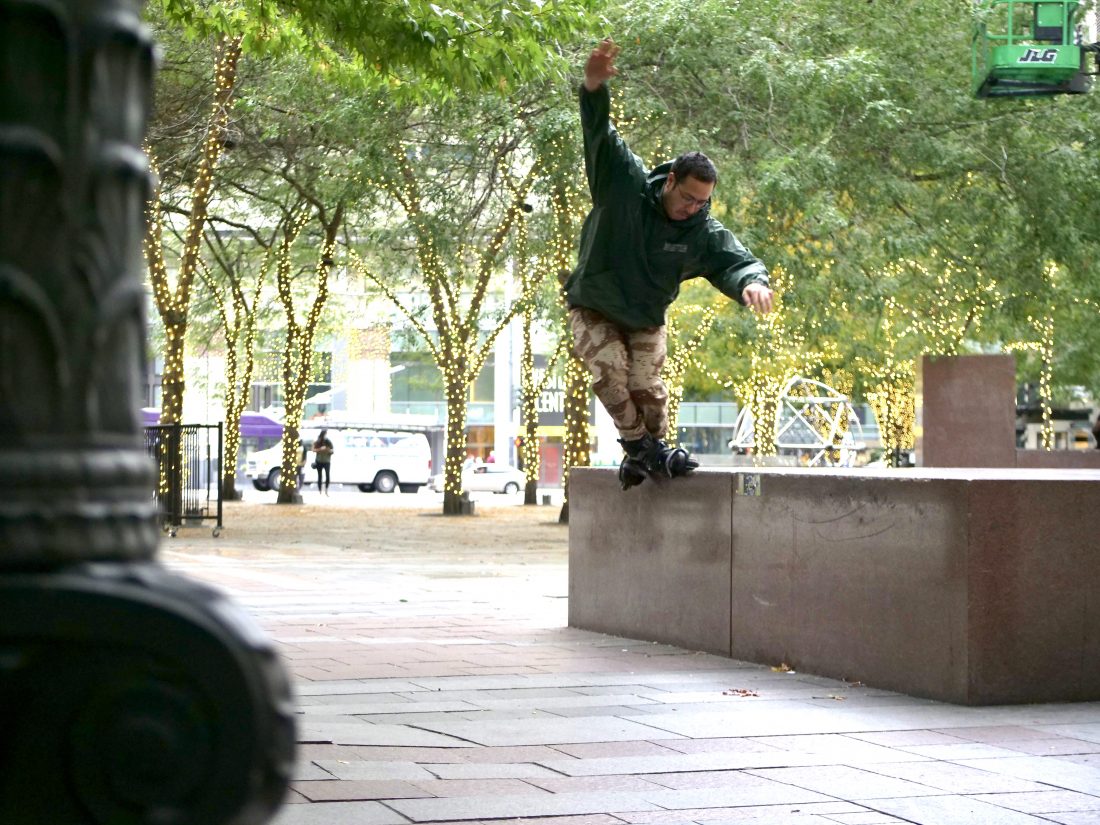
ALLEY OOP TOP PORN BY MATTHEW EZIASHI – @MEZIASHI
KL | So with your mechanical engineering degree and previous experience in design, how has it assisted you in creating the Masterblade, which is a frame that is quite different than other frames that are currently on the market?
KS | In both my education and work experience I have learned the importance of using root cause analysis and intention driven design when designing a product. Basically, try and take the simplest approach to achieve a purpose based design. I looked at all the frames that I’ve skated over the years and picked all of the features that I liked from each and combined them into a frame that I thought would suit my own skating perfectly.
KL | I couldn’t help but see certain design elements of the Masterblade frame that seem loosely inspired by your fixed gear bike work. Do you feel the frames are at all reminiscent of bicycle design? ( I am sure your experience could only have helped in the developmental process.)
KS | Good observation! Yes, there are definitely parallels to be drawn between my process between the two. In designing for bicycles, all changes in geometry have direct correlations to how the bike rides. For example a bicycle with a short rear end will pop up easier for manuals or wheelies—too short though and you run into clearance issues with the rear wheel and sprocket. A steep head tube angle makes the bike handling much more “twitchy” and also makes nose manuals easier. However, if you go too extreme with the headtube angle, and you lose barspin clearance and the handling of the bike becomes un-rideable. When designing a bike, you have to find a balance in what you’re trying to achieve with the geometry and weigh that against any negative consequences those design choices might have. It’s all about design optimization!
When I set out to make a design for these frames I made a mental list of all of the features I wanted to incorporate into the final design. To me the perfect frame needed the following:
- Stiffness and speed- achieved with a flat wheel setup, 60mm outer wheels, aluminum frame cores, and integrated frame spacers
- Low standover height- Achieved by recessing the wheelwells in the boot
- Large H blocks- Achieved by using 47mm inner wheels spread as wide as possible
- Fast sliding- Achieved by using machined delrin on grind surfaces
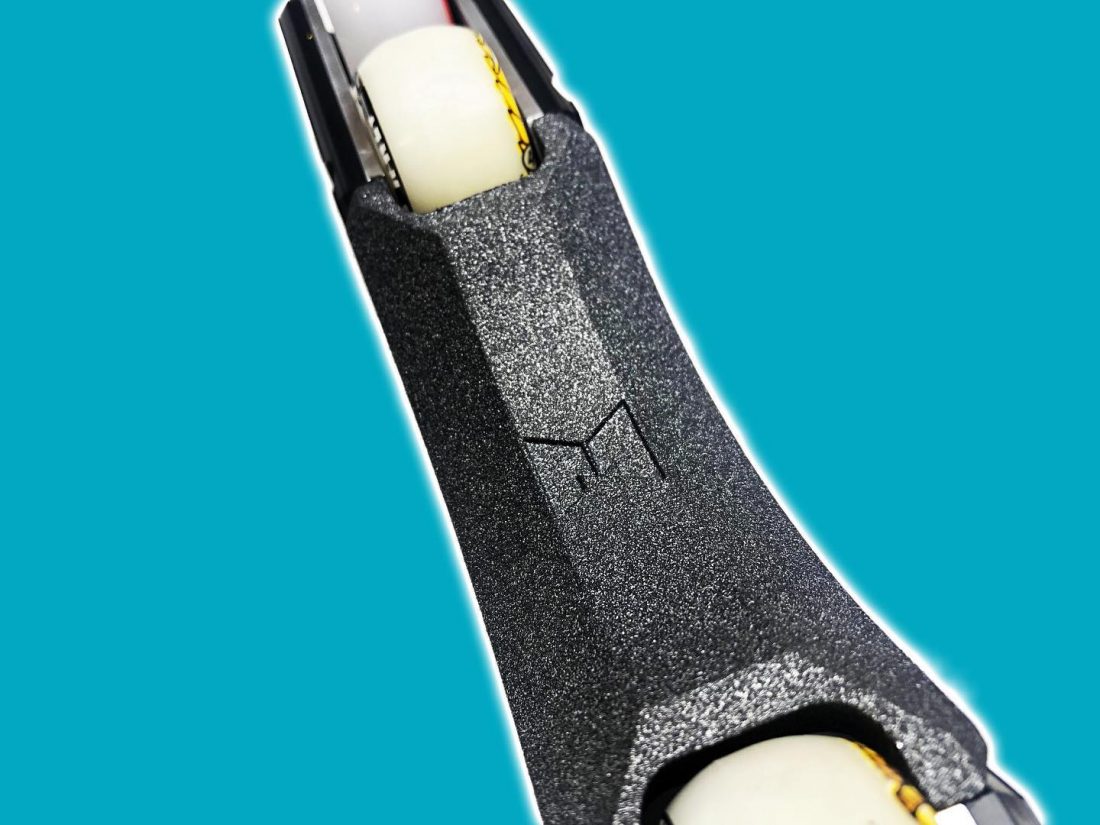
KL | In your experience in developing the frames, do the vented sidewalls make a noticeable difference in the grinding performance or overall weight of the frame?
KS | To be honest, I don’t think that the vented sidewalls make too much of a difference when it comes to how fast the frames grind. I think material choice is what has the greatest effect on grinding performance. I added the cutouts to reduce weight plus it looks kind of cool to see your wheels spinning haha.
KL | Was there any concern to your frame vent on the sidewalls possibly “catching” while grinding certain rougher surfaces?
KS | I haven’t noticed any problems with catching even on rougher surfaces on these frames versus a traditional closed frame.
KL | The internal structure of The Masterblade frame is reminiscent of the 50/50 Core or Kizer Element 1 frames that were quite ahead of their time. Can you give us a little insight into the material that was used for the internal core and outer sidewalls and the skating benefits of using dual materials ?
KS | The Kizer Elements, 5050 Cores, and to an extent, the never released Epoch frames were definitely big inspirations for the construction of my frame. Using an aluminum core gives you a huge rolling speed and stiffness advantage over a traditional plastic frame. However, grinding directly on aluminum doesn’t feel very good to me so it seemed logical that I’d use a fast sliding plastic on the grind surfaces of the frame and pair them with metal core to have the best of both worlds. I am using 6061 aluminum for my cores and machined delrin for the wear faces of the frames. 6061 is a good choice because it is a common material which is lightweight, easy to machine and strong enough for aggressive skating. I chose to use delrin (acetal) rather than UHMW for the grind surfaces because in my experience, UHMW has a tendency to warp after use whereas delrin is a bit stiffer and has similar properties when it comes to sliding/grinding. UHMW is also more difficult to machine and it is much harder to get nice surface finishes when compared to delrin.
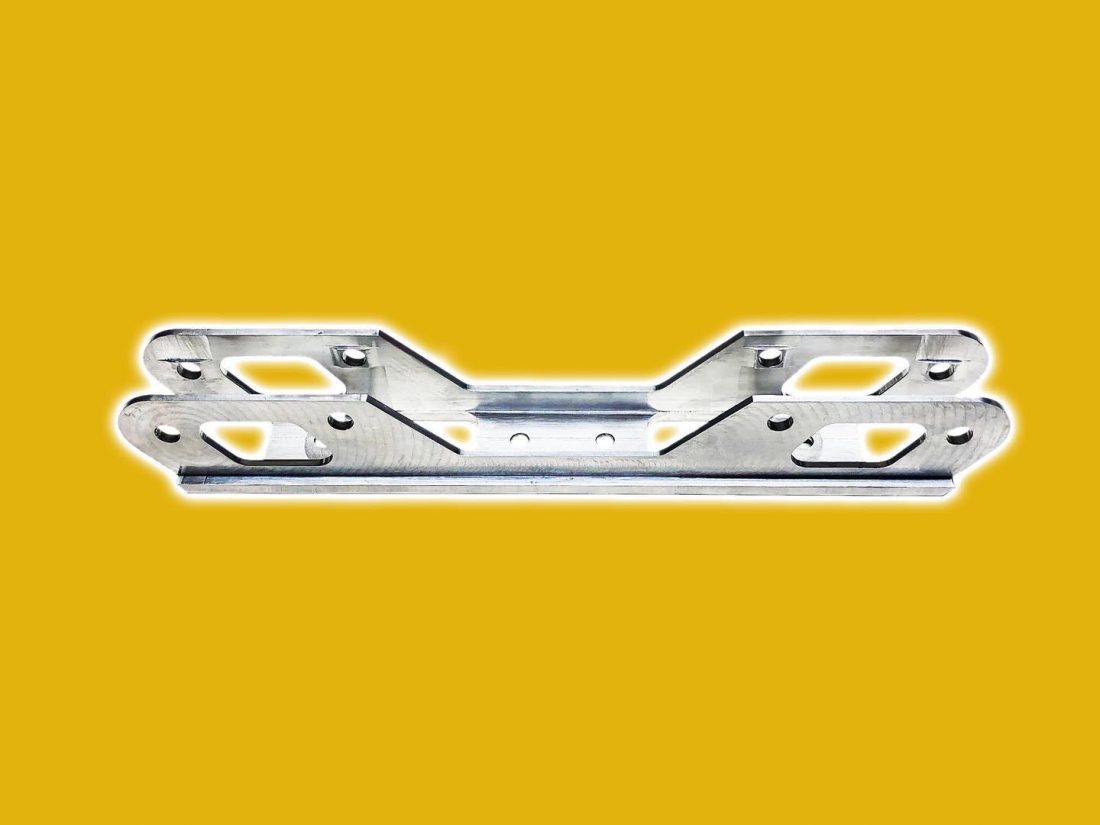
KL | You have decided on two different frame lengths (I would assume small 255mm = 6-9, large 270mm = 10-13 ) for the initial start of the frame, do you have any intention of expanding those to smaller or larger sizes? Or does it really depend on customer demand?
KS |I think for now the 255 and 270 will be the sizes I’m gonna go with. If there’s enough demand for smaller or larger I would definitely consider making more sizes though, it’s really just a matter of financially justifying producing those sizes. Big/little foot skaters, shoot me a DM if this is something you think you’d like and maybe another size could be considered in the future.
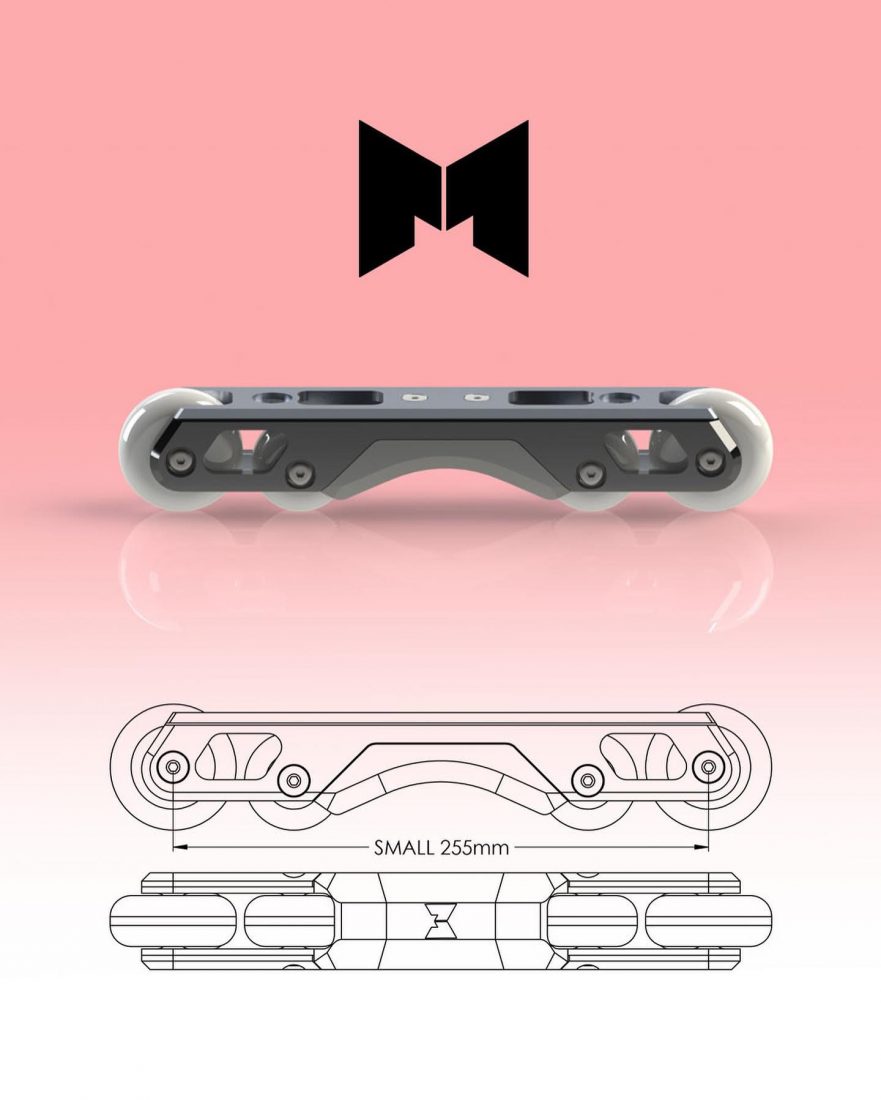
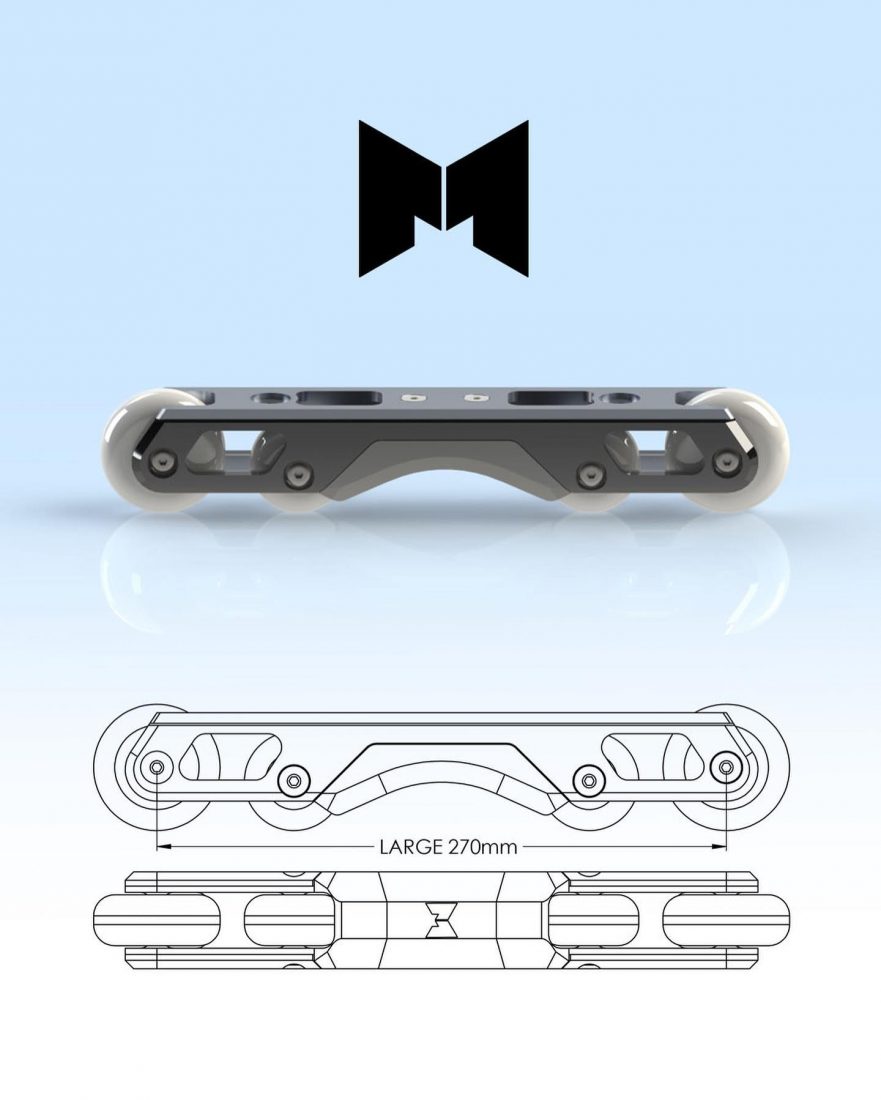
KL | So in hearing your interview with Ricardo Lino recently, you discussed how having two ACL injuries was partly the cause of your decision to design a frame with a lower ride height. Did you experiment with different frame lengths and heights in developing the frames or based on your personal preference did your design tend to lean more towards a shorter frame height and standard length? (Considering the large demographic of older bladers, this might be a great selling point for you! )
KS | Haha yeah! I’ve got full ACL tears in both knees. I was told by my doctors that I didn’t need to have them surgically repaired because the muscles around my knees are strong enough to hold my knees together presumably from all the cycling and skating I do. That said, having these knee injuries makes crouching down super low on grinds pretty uncomfortable. When I was skating the kizer elements I really didn’t like how tall they were specifically because when doing topsides or royales/farves I’d have to bend my knees super low to properly lock the grinds which felt terrible. So having a low standover height on the frame was a priority for me. I designed my frame to be 56mm from the ground to the bottom of the boot/soul using 60mm wheels (this is the same concept that the Aeon boots employ). This lets me get away with using more ankle flexibility in locking topsides and groove tricks. I checked the “What frames” website and I’m pretty sure my frames are the lowest standover UFS frame on the market currently even when using 60mm wheels!
KL | What is the maximum outside wheel height in the Masterblade frames? Will you need to do any kind of modication to the soul plates to ride these frames? ( I know this may vary depending on what skate the user is riding)
KS | The frames are designed around a 60mm outer with a 47mm inner wheel pairing, 58mm and 45mm will also work. As far as I know every skate other than the Adapts will need the wheel wells recessed with a dremel or bench grinder. On 60mm outers you’ll need 4+ mm of material removed above the front and back wheels.
KL | It seems like it would have taken some time to find the right outer wheel profile to match the anti-rocker wheels and not compromise the feeling of rolling on a flat setup. Of all of the setups that you tested, which were the ones that you felt fit the Masterblade frame the best?
KS | Yeah finding wheel combinations was a huge pain in the ass. I’d been skating the same setup for the last few years and I hadn’t really paid too close attention to what was new in the skating industry. It was a bit of a surprise when I found out that there are very few current options for 47mm antis. I also realized that wheels are coming out in a ton of different profiles as well these days which has a huge effect on how these frames ride. I purchased something like 15 different sets of wheels to find the perfect combination.
I found 3 different setups that worked well:
- Undercover square profile 58mm (age cured or Enin) with Gawds 45mm antis
- Undercover 60mm Apex with 47mm Revision Clinger hockey wheels (not currently recommended)
- 50/50 60mm outers with Eulogy 47mm inners- This combo had the best profile match and is probably my current winner in terms of pairing with my frames.
KL | There are noticeable limitations in availability of anti rocker wheels these days, and even fewer options for different sizing, profiles and hardnesses. This issue actually forced you to turn to roller hockey goalie wheels, how was your experience in using those paired with your frames?
KS | The Revision “Clinger” hockey wheels felt incredible initially. They were super fast and super grippy and were a perfect match for the UC round profile. However, after a hard park session on these wheels the 47mm middle wheels had all cored.
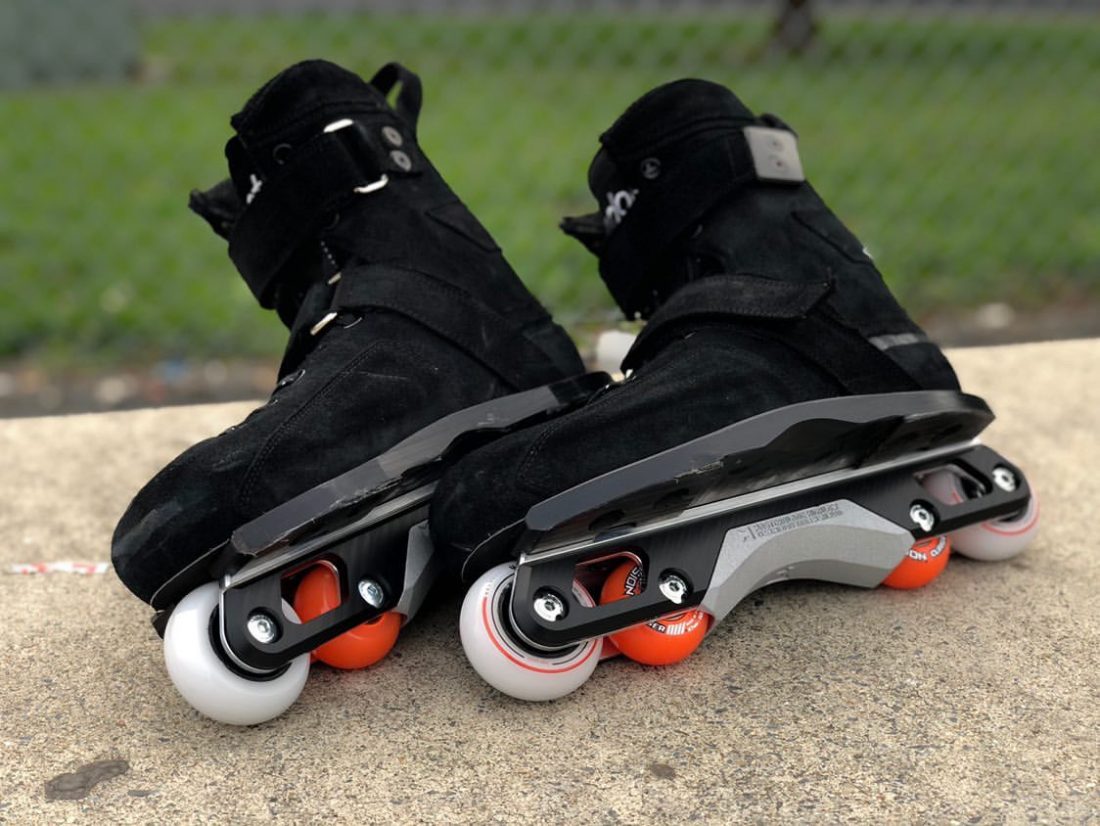
KL | I also hear talks of you developing a softer anti-rocker than is normally produced, which would be made specifically to be paired with the Masterblade frame. Can you go into more detail about that?
KS | I am working with the manufacturer of the Revision clinger 47mm wheels to produce a core-less 47mm anti wheel using the same mold/profile in an aggressive compound. The plan is to have these poured somewhere between 95-97A durometer in order to still have the rigidity needed for a core-less wheel but still have a good balance between grip and slide. I think this will be the final solution for a perfect pairing with the UC apex wheels which I am in love with.
KL | Do you have any plans on growing the Masterblade frame company further like creating a team to promote the company?
KS | I’m taking this project step by step. I would love to eventually get to the point where I could sponsor some riders or even offer other aftermarket products!
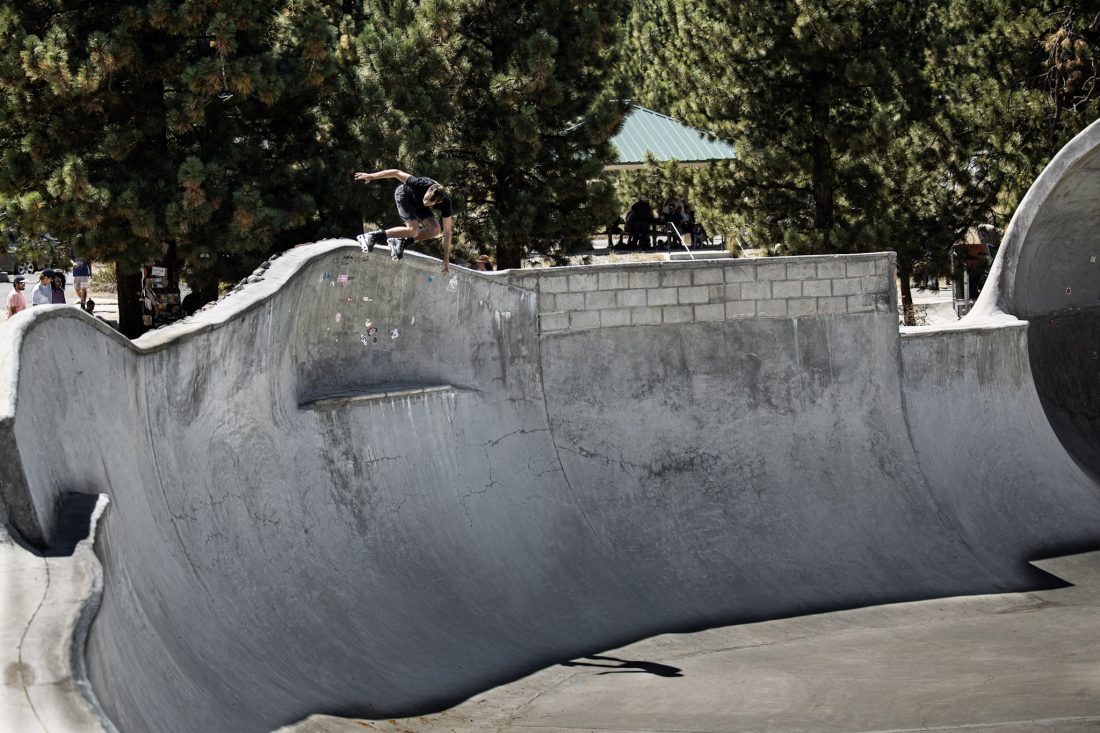
PHOTO – ERIC ESQUIVIAS @ESQUIVIAS_LENS
KL | Thank you Kareem for taking the time to do this interview. Is there anyone you would like to acknowledge or thank for their assistance in making the Masterblade frame a reality?
KS |I definitely couldn’t have done this without a lot of help. Huge thanks to my homie Tait for helping machine my first prototype pair of frames. Wouldn’t have been able to do this without him. Also a big thanks to all of the folks who bought the initial batch of production frames. It is really cool that people are willing to try something new. Also, Gumby and Todd M. for all the testing and feedback. Big shoutout to Ricardo Lino for helping to support this project and help me get the word out about them. Matthew, Preston, Allen and Brian for helping film my Masterblade part. All my Dale boys, Master Bike Co. boys and fgfs and blade homies. My parents, brother, and girlfriend for their help and moral support! Also big thanks to you, Kevin, for giving me the opportunity to talk about this and Be-mag for all of the support over the years!
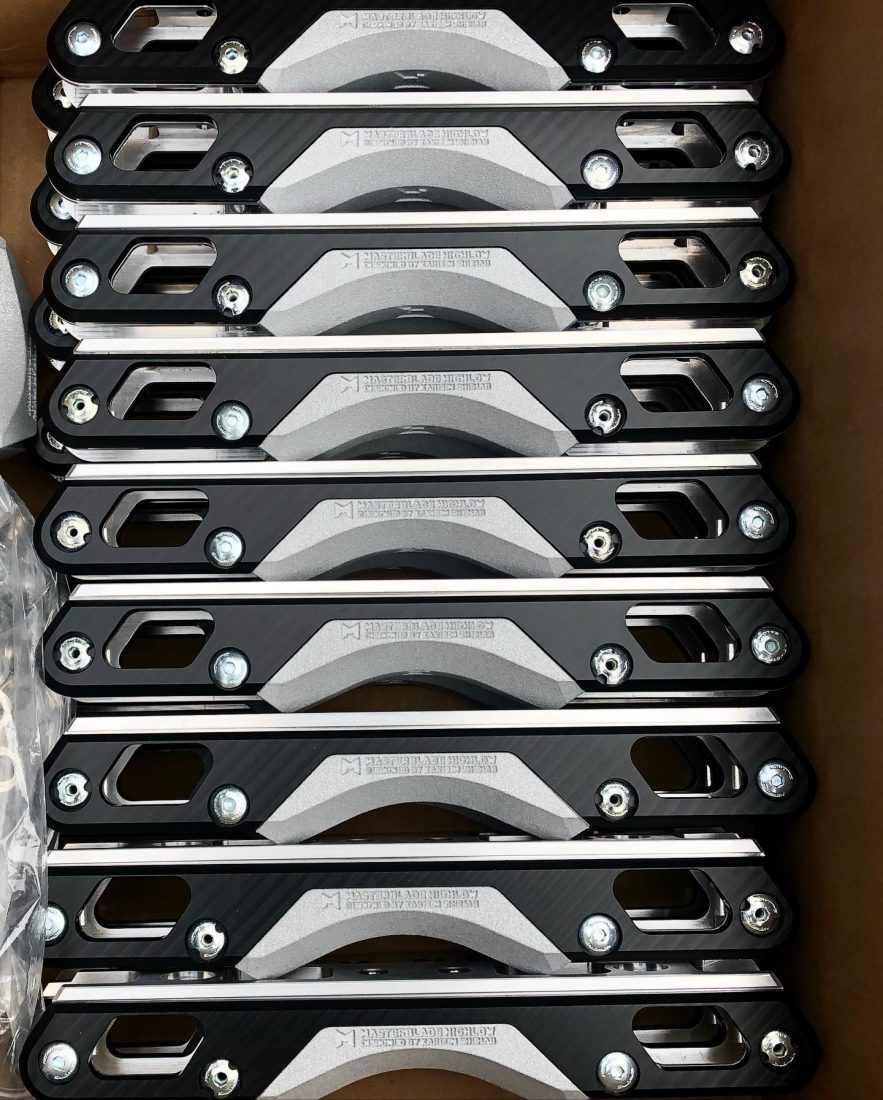
PRE-ORDER THE MASTERBLADE FRAMES AT WWW.MASTERBIKE.CO
BE SURE TO FOLLOW KAREEM @KILLAKAREEM & MASTERBLADE @MASTERBLADECO
YOUR FAVORITE PRODUCTS BY YOUR FAVORITE COMPANIES. SUPPORT BE-MAG WITH EVERY PURCHASE.
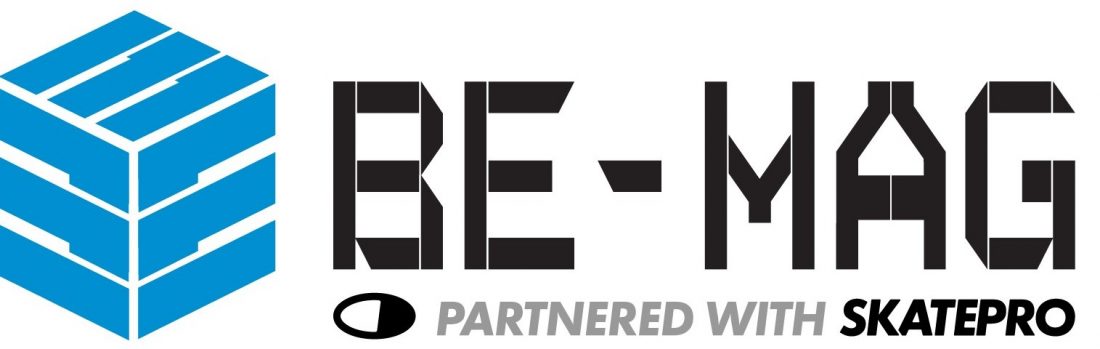